Five steps to build a culture of process improvement and continuous change and realize sustainable productivity results.
Axsium’s industrial engineers and workforce management specialists have spent decades identifying and implementing process improvements for our customers.
Regardless of whether process improvement is the primary focus of a project or a value-added opportunity that we uncover along the way, the Axsium team is always on the lookout for improvement opportunities. In fact, we encourage our clients to adopt the same mindset.
We have translated these insights and experiences into five straightforward steps to help your organization get started:
- Step 1: Get to know the proven methods
- Step 2: Get acquainted with the tools
- Step 3: Get your ideas prioritized
- Step 4: Get testing in the field
- Step 5: Get ready to adopt
In Part 1 of this blog series, we surveyed the history and current landscape of process improvement philosophies and methodologies. Now, we will take a deeper dive into the specific tools and best practices our engineers recommend.
Step 2: Get Acquainted with the Process Improvement Tools
Our consultants use a wide range of tools from their formal industrial engineering education, as well as tips and tricks acquired through years of retail and hospitality experience. These tools include some you may have heard of, such as Standard Operating Procedures (SOPs), and others you may not have, like Value Stream Maps (VSMs).
It’s critical that you understand when and why to use these tools. In this blog, we will explain how to use them across three common phases of process improvement ideation: Brainstorm, Observe, and Analyze.
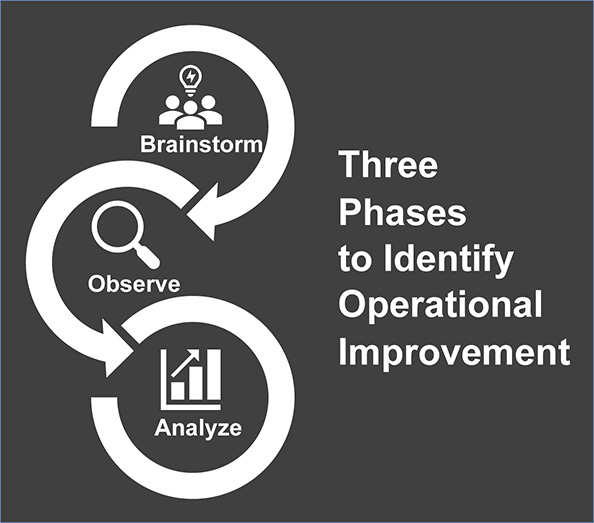
Brainstorm with a Cross-Functional Team
Axsium’s engineers kick projects off with a healthy amount of brainstorming to get the process improvement juices flowing. During discovery workshops, we work alongside client subject matter experts (SMEs) from all levels of the organization. Together, we work to understand and document current processes and identify pain points and potential improvements.
We often find opportunities for process improvement when there are inconsistencies between Standard Operating Procedures (SOPs) and on-the-ground operations. While head offices typically develop SOPs, field level SMEs perform these tasks day-in and day-out. This makes those SMEs well-positioned to suggest alternative approaches, particularly when it comes to the nuances of ever-evolving retail and hospitality work environments.
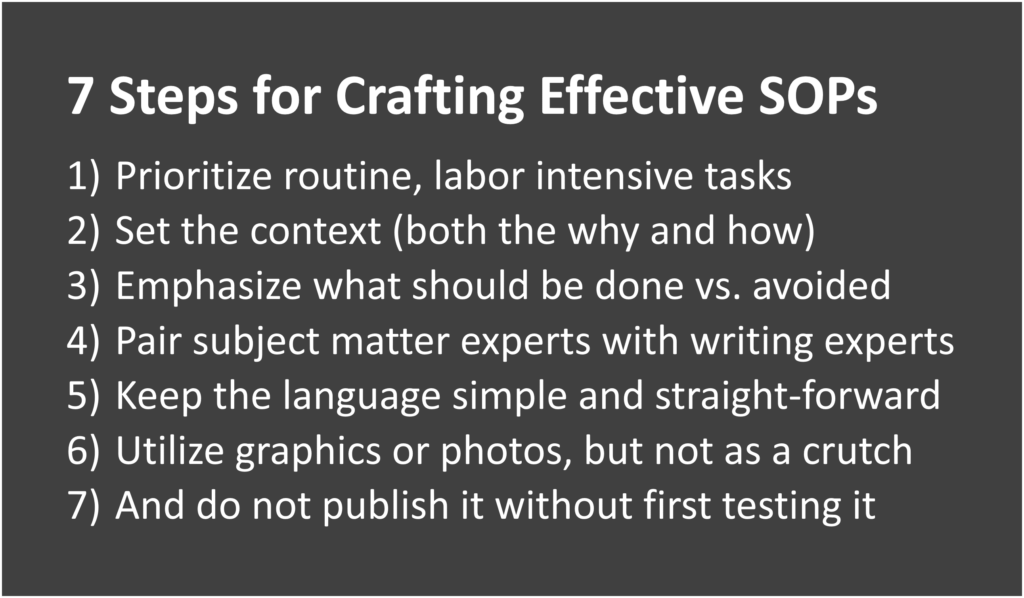
Another effective brainstorming tool, Value Stream Maps (VSMs) are a form of process map. Our team focuses on each step of the process in question to evaluate the value it provides to the customer. This makes waste and unnecessary steps easy to spot.
We recently documented a client’s as-is inventory process. The manager would first log a written count and later manually enter all the information into their back-office computer. The redundancy seems obvious in retrospect, but the client was convinced these steps reduced errors and gave their managers the flexibility to start and stop the process. Using a VSM, we isolated the problem steps and identified alternative tools (e.g., tablets, laptops, or handhelds) to maintain accuracy levels while eliminating the need for double processing.
Onsite Observation and Optimization
Axsium’s experienced engineers arguably provide the most value to clients through the act of observing work performed onsite. As outsiders, they can identify wasteful or inefficient processes without bias or preconceptions. But we don’t just focus on the current task at hand. We know our client’s employees don’t perform their work in a silo. Our engineers take a 360-degree view of the operation to fully contextualize process improvement ideas.
5S is one of the most common onsite tools our engineers use during the observation process. Part-philosophy and part-practice, 5S is a Japanese methodology which translates to Sort, Set (In Order), Shine, Standardize, and Sustain. The primary goal is to clean and organize a space to eliminate the need to search for items. This is especially common when backrooms or other high-traffic, high-touch areas like kitchens or front of house spaces are the focus of a 5S study.
Recently, an Axsium engineer noticed during observation that employees were looking in several locations to find all their cleaning supplies. Once we implemented 5S, the client stored and labelled all their cleaning supplies centrally, saving significant travel and search time.
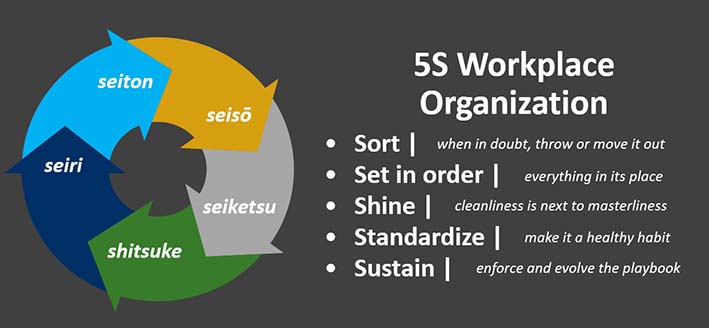
A 5S exercise is often the first step or the main initiative of a Kaizen event. Easily confused with the Kaizen philosophy which we covered in the first installment of this blog series, a Kaizen event is a multi-day (sometimes week-long) exercise. During a Kaizen event, we break down a process, eliminate any unneeded elements, and then re-implement it more efficiently.
While a leader facilitates the event, those working in the area every day make up the majority of the team. Once we have observed an area, it’s vital to bring on-the-ground workers into the improvement and implementation planning effort. They have valuable insights into what is and isn’t working.
Offsite Review and Analysis
While structured events are ideal for improving local environments, it’s impossible to organically capture every process improvement opportunity while onsite. Therefore, our team relies heavily on repeatable labor study techniques to retain and reproduce what they observe for later analysis. Our two preferred techniques for this are video capture and activity sampling.
Video capture lets us break down processes into individual steps to understand their overall impact using a Predetermined Motion-Time System (PMTS), which contain globally accepted time values for an average person to perform basic functions. These time values are based on body motions (e.g. walk one step) as well as the movement of objects (e.g. wipe down a surface with a cloth).
Software solutions like Axsium’s Opus contain libraries of work measurements and built-in reporting to help expedite this process. They help you spend more time analyzing improvement opportunities and less time on data capture.
For example, we noticed while analyzing video of a clothing retailer’s cash wrap that the cashier was storing hangers in a box to rehang later. Using Opus’ PMTS, our engineer proposed an alternative method of placing hanging racks between two registers, eliminating the double handling.
Activity Sampling is another efficient technique to highlight and quantify potential process improvements. Using Activity Sampling, we take samples at set intervals to estimate how much overall time employees are dedicating to specific tasks. These samples include the tasks employees are doing, their assigned role or job, and where they are completing tasks.
Mobile tools like Axsium’s Studia are purpose-built to collect samples across a representative range of locations, days of week, and times of day. With less time spent on manual data entry, we can dedicate more time to analyzing the results and identifying potential improvements.
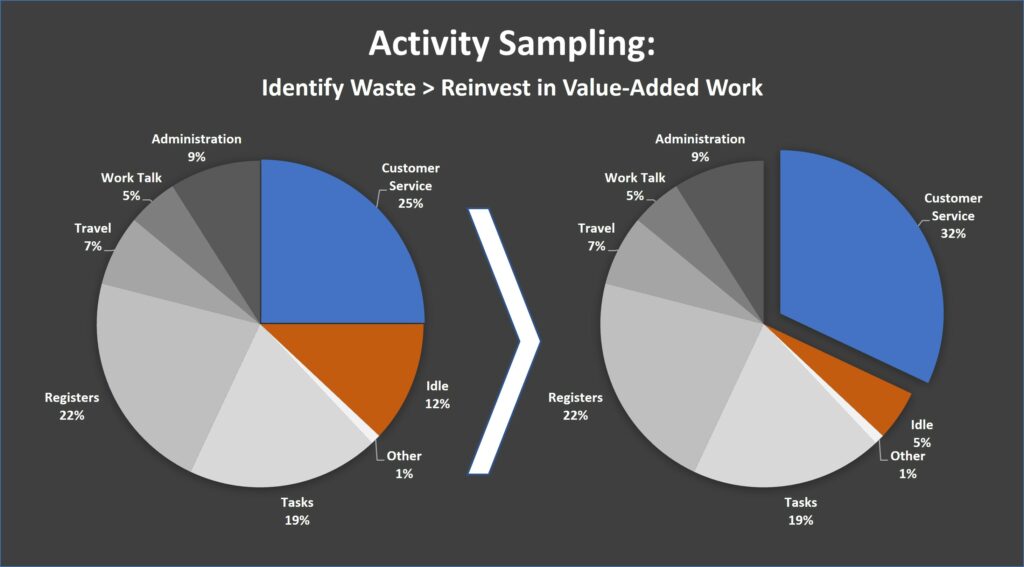
For example, understanding where and when idle time is especially high can help you to repurpose it. Analyzing the activity sampling results can provide insight into why, where, and when the idle time is occurring and suggest value-added activities that employees can perform instead.
What’s Next?
Employing our recommended tools across the brainstorm, observe, and analyze phases of process improvement will consistently lead to insights and ideas to generate efficiencies and reduce waste. Have questions? Wondering how to get started? Our labor productivity experts are ready to help out. And we’ll be back in the coming weeks with Steps 3-5, where you will learn how to get your backlog of improvement ideas prioritized, tested, and ready to adopt!