Labor budgeting and planning is all about finding the right balance between giving your locations the labor they need while meeting long-term financial targets.
Inevitably, this pits Operations and Finance against each other in a friendly tug-of-war. Both sides are driven by the same goal: to do what’s best for the company. But the labor metrics and budgeting approaches they use are often worlds apart.
The Financial Labor Budgeting Wants
At most organizations, Finance teams develop a company-level budget by projecting year over year sales growth and indexing that against the expense rates required to meet overall profitability expectations.
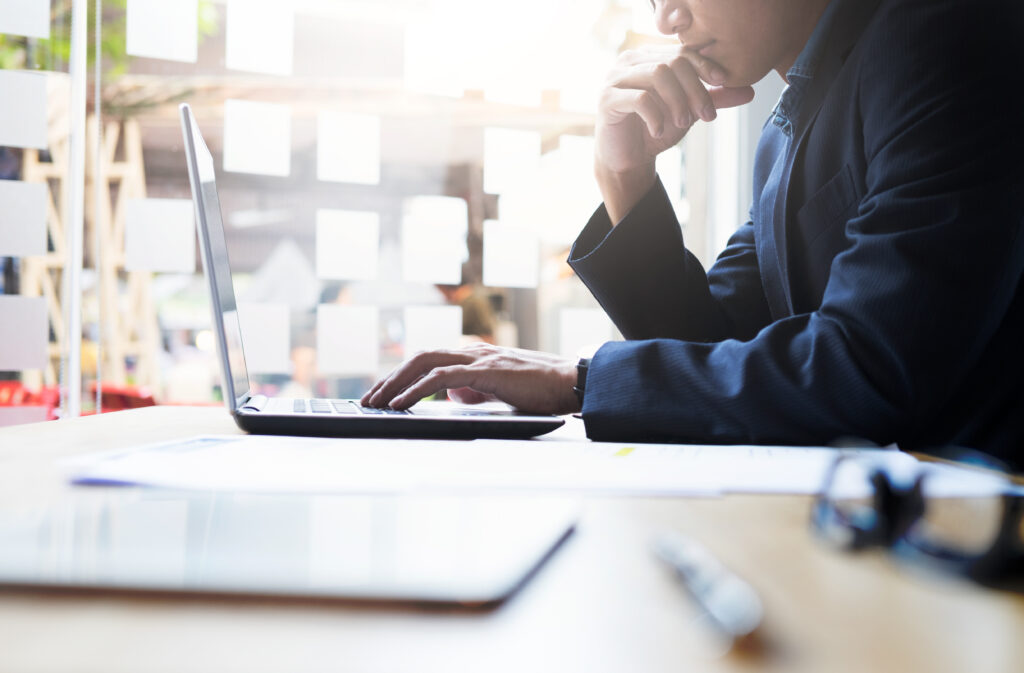
The process bakes new initiatives, location growth, and other strategic goals into anticipated revenues and costs. Of course, this makes the budget the cornerstone your organization’s plans to achieve its financial targets.
But what about the labor elements of that larger budget? Unsurprisingly, Finance tends to rely on a “Top-Down” rationale for goal setting. Corporate labor metrics are tightly linked to sales, using factors like Rate of Sales and Sales per Labor Hour.
“Our targeted labor expense rate of sales is 10%. That means if we are going to sell $X we will allocate 10% of $X in labor.“
This is a sensible way to establish macro-level goals for the year. But it doesn’t inherently capture the on-the-ground reality for the hundreds or thousands of locations an organization may operate.
Simply put, top-down budgets lay out the outcomes you want to see. But to realize these goals at an individual location level or across the weeks of the year, you have to consider the resources your locations need to succeed.
The Operational Labor Budgeting Needs
This is where the Operations team steps in. Operations’ typical “Bottom-Up” philosophy is firmly based on the real-world requirements to successfully operate each of your locations across the seasonal swings of the year.
Financial budgets are clean and simple. But building an accurate representation of each location’s labor needs for each week of the year can be as messy as, well, reality itself. Operators need to pull together a host of inputs. These include Business Volume projections, activity-based Labor Standards, Location Characteristics, and staffing rules such as Min/Max Coverage requirements.
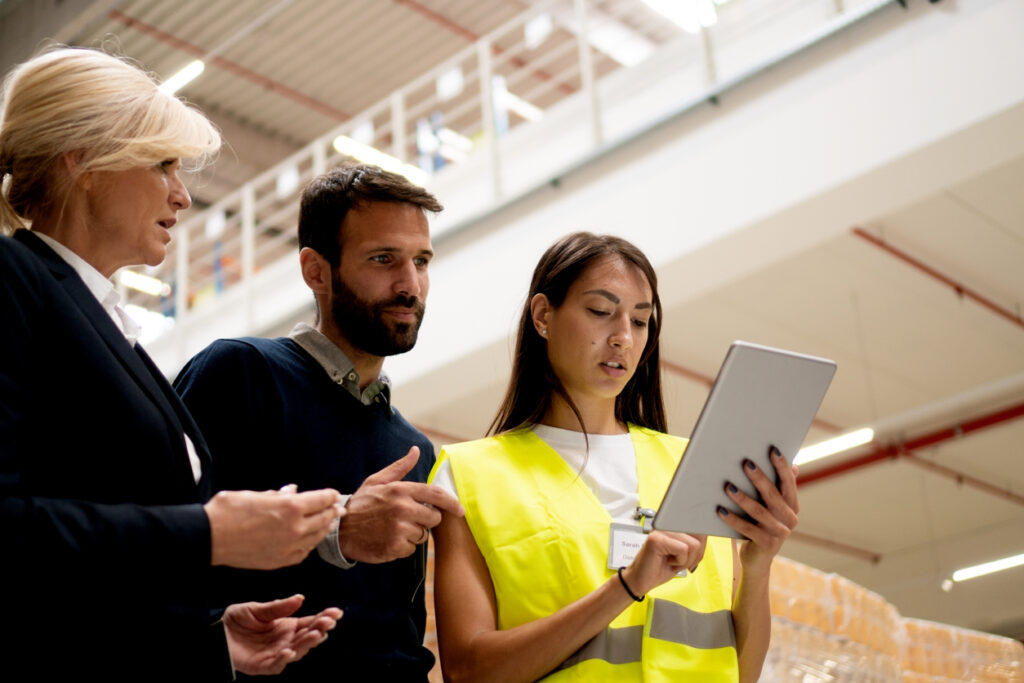
These essential building blocks help Operations pull together a labor plan that avoids the wastefulness of overstaffing, or the perils of understaffing your locations.
“Not all revenue is created equally. Our locations all have different labor needs. Those differences need to be reflected in the way we build our labor budget.”
Most organizations can leverage this model to schedule a few weeks out. However, generating bottom-up labor projections for a full year (or more) with the same level of precision often proves difficult. The approach typically involves cobbling together spreadsheets and access databases, creating a complex, disconnected, and error-prone process.
Combined, these factors cause many Finance leaders to approach Operations’ bottom-up labor numbers with a healthy dose of skepticism. And the net result is a slow, frustrating, and sometimes contentious labor budgeting process.
Of course, there is wisdom to be found in both approaches to planning for labor. The question is: how do these two different teams come together? By learning to speak each other’s language they can build a budget that works for the entire organization. But how do you find that balance?
Aligning “Top-Down” with “Bottom-Up”
While it might sound daunting, in reality this challenge may not be as hard as it sounds.
The vast majority of Axsium’s clients already have advanced bottom-up planning processes. But there’s a missing link. The teams responsible for top-down financial planning don’t have this information at their disposal. And they lack faith in the tools used to generate the numbers.
Organizations that want to master the labor budgeting process need to increase transparency and improve collaboration between Operations and Finance:
- Finance needs visibility into how Operations is calculating its bottom-up numbers
- Operations needs to incorporate top-down assumptions from Finance into their models
- Both teams need to speak the same language and work toward the same outcome metrics
- Both teams need the ability to rapidly analyze assumptions and simulate planning scenarios
What Next?
When both teams understand each other’s needs and priorities, they can work together to build a labor budget that works at every level of your organization. And this new budget won’t just be better for the company. The path to getting there will have been faster, more collaborative, and ultimately better for the bottom-line.
On May 30th, Axsium announced the release of Planara, our powerful new labor planning and analytics solution. Get in touch to find out more about what is shaping up to be a game-changer for your Finance and Operations teams. Or register for our upcoming webinar on July 14 and explore a live interactive demo environment.