Many retailers experience a mismatch between the number of labor hours they forecast and the actual number of labor hours they need to properly serve customers. Labor minimums are often a large part of the problem.
In a perfect world, if you had 23 hours of customer service to perform, you would want to staff 23 hours of labor. But we all know too well that the demand curve in a retail environment is far from smooth. Seasonal, weekly, daily, and hourly fluctuations can make labor forecasting unpredictable and inaccurate. The one constant in all this is the baseline number of employees that you need on-site to keep your store operating. This is your labor minimum.
When you’re building a labor forecast, you need to keep a close eye on your labor minimums. At Axsium, we see retailers use a variety of approaches to setting minimums. It can be surprising how dramatic an impact these different methods can have.
Approaches to Labor Minimums
Some use weekly staffing minimums (or base hours), but don’t consider the tendency to top-up based on the daily or intraday shape of trade. Others look at the weekly shape of trade and set daily labor minimums, while others don’t set minimums at all.
You want to produce an operational plan or budget that reflects the true interaction of your labor standards and staffing minimums. To do that, you need to forecast labor demand at the most granular level possible. This is where many workforce management solutions and Excel-based models functionally fall short. It’s also where your finance team may tend to conceptually overlook things.
To understand why, let’s look at three different approaches to this process, each at a different level of forecasting maturity, that yield three very different labor forecasts.
Maturity Level 1: Not Setting Labor Minimums
When they don’t require minimums, most retailers allocate weekly labor without adjusting for any shape of trade. In this case, you would usually set the budget a certain percent higher than you need to ensure there are always enough hours to cover customer demand.
As you can imagine, this can be an extremely imprecise practice, often leading to significant staffing overages on some days and shortfalls on others. This is the least sophisticated method of looking at your staffing. You should avoid it if possible.
Maturity Level 2: Setting Labor Minimums Based on Weekly Shape of Trade
For a more complex scenario, let’s assume your store is open for 78 hours a week—12 hours from Monday to Saturday and six hours on Sunday. Your business rule states that you always need a headcount minimum of two per hour. Your weekly minimum hours calculation, or the total number of hours to be filled, is then 156 (2 x 78).
Coincidentally, your labor model forecasted that you would need 156 labor hours this week. You’d be forgiven for thinking that your labor model has forecasted enough hours to cover your week.
However, things change when you allocate your 156-hour forecast across each day based on their share of trade. As you can see in Figure 1, some days fall below the minimum amount of labor required to cover them.
If you staffed your store solely according to your labor forecast, you would fail to satisfy your business rule of having two employees on-site from Monday to Friday. More importantly, it also means that the budget from the forecasted labor will be lower than you really need.
Weeks 02 and 03 in Figure 1 fall below the minimum 156 hours. They will likely get topped up with no understanding of which days the shortfall is happening.
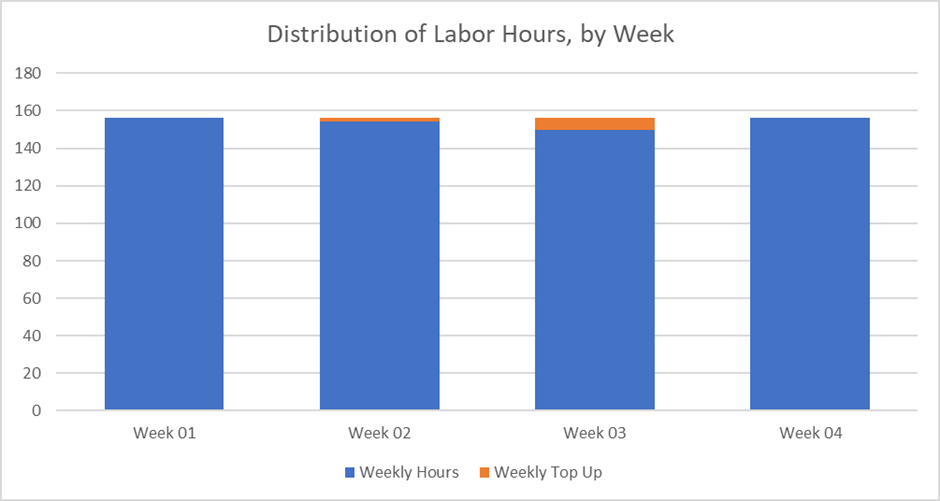
To fix this shortfall, as seen in Figure 2, you “top up” your labor hours. This ensures your total trading hours for the week are covered with at least the minimum amount of labor per hour. You get a slightly more accurate picture of your total labor requirement. That requirement includes 156 hours of forecasted labor and 17.3 hours of top-up, for a grand total of 173.3.
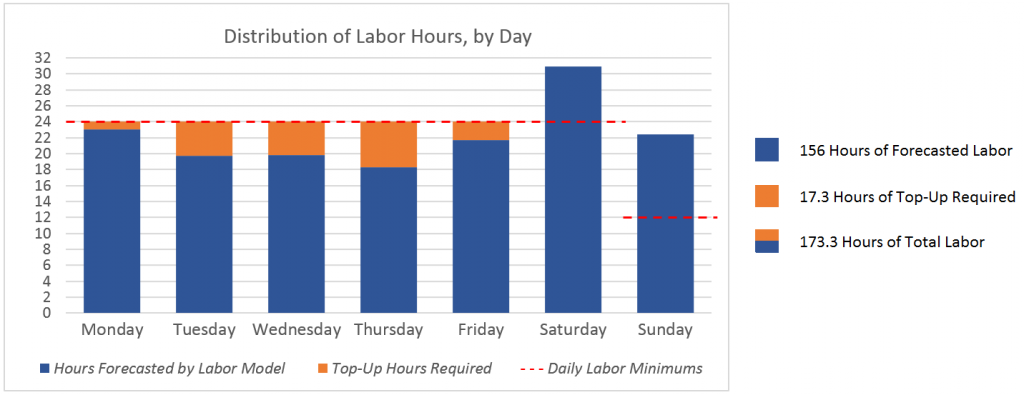
Maturity Level 3: Setting Labor Minimums Based on Daily Shape of Trade
An even more sophisticated way to calculate labor minimums is by day. Using this approach, you top labor up to cover the trading hours you need to operate the business for each day.
Let’s take Monday, for example. Recall that in Figure 1, we saw that there was a shortfall of about one labor hour on Monday. But let’s look more deeply into the hour-by-hour shape of trade.
As you can see in Figure 3, the hourly view paints a very different picture of how much labor you need to top-up. You don’t need one hour of top-up—you need more than 10! If you repeated this analysis again for the other six days, you would identify over 50 hours of top-up. You would likely have missed those had you only been looking at the weekly shape of trade.
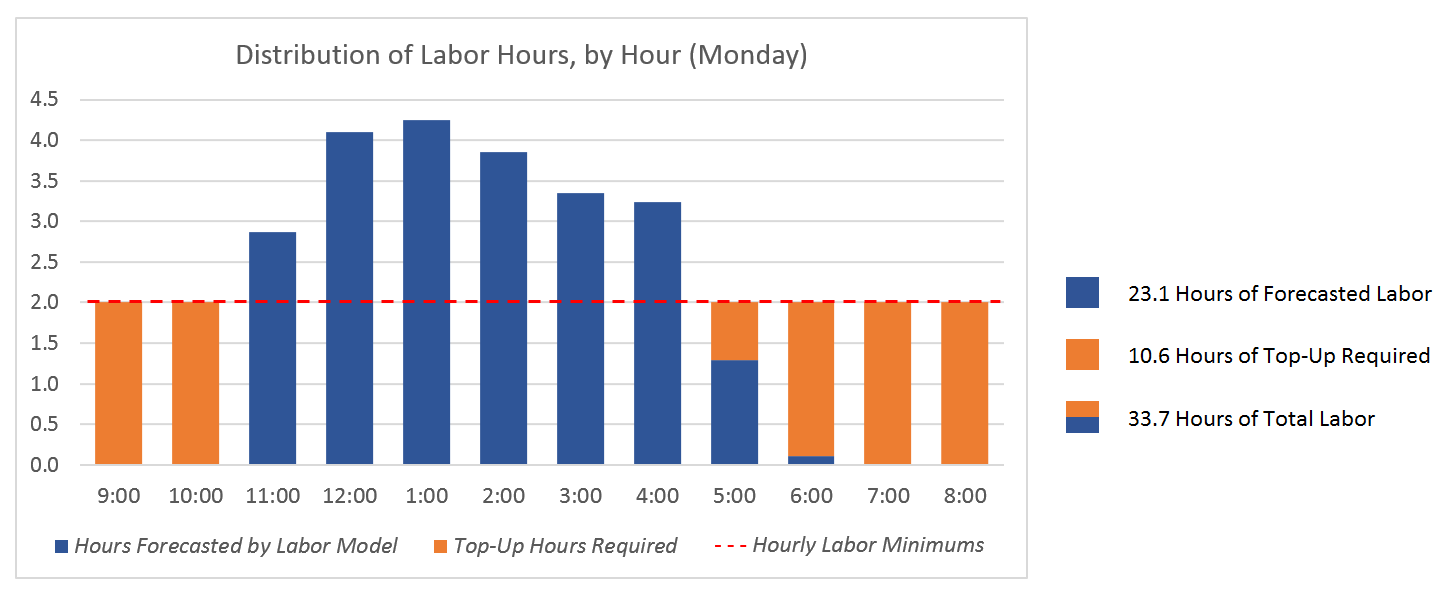
So, What Does It All Mean?
There’s an important lesson here. The more granular you are in your approach to forecasting and setting minimums, the more accurate your labor requirement. In our example, the third model discussed above gives you that detailed approach to provide a better forecast.
When you employ the right labor requirement consistently, you’ll be better able to manage operational costs. You’ll reduce the number of times you’re over or understaffed and re-engage employees who may have been impacted by incorrect staffing levels in the past. Most importantly, you’ll delight your customers by providing them with the level of service they deserve and expect.
You can see how important it is to create the correct minimum top-up allowances. It’s even more important if you export the hours your labor model calculates to a scheduling application that has a minimum coverage function.
That said, forecasting labor and setting staffing minimums should never be a one-size-fits-all routine. Rather, you need to consider each store’s history, as well as its customer demographics, store type, special days/sales, etc.
Essentially, you may have overriding rules (like one-two-two coverage) that span your entire chain. Regardless, you will be best served by adapting those rules to your stores’ specific needs, seasonality, and special events. It’s nearly impossible to do this and model the shape of trade in Excel or a home-grown solution at the hourly or even quarter-hour level. You need to manage this job in your WFM system, since it deploys labor using the intraday shape of trade.
How We Can Help
No matter which maturity level you’re at now, Axsium can help you ensure that your labor model is accounting for minimums in the best way for your business.
We analyze a broader set of stores and recommend/configure updated staffing rules in your WFM system. Some of these may dynamically change with different events or seasonality. Managing at this level of store-specificity does require additional overhead. But it will help you guarantee you are deploying labor optimally throughout the day, week, and year.
Reach out to us anytime to discuss how to optimize your unique labor model.